Test Results
The non-accelerated corrosion control performance test procedure is presented below.
- Factory sealed ground finish steel Q-panels are removed from their package and are wiped down with acetone to remove the corrosion inhibitor applied by the manufacturer.
- The Q-panel is treated once with a bulk lubricant.
- The Q-panel is mounted on a rack with all of the other Q-panels.
- All of the Q-panels are exposed to full sunlight, rainfall, and a condensation cycle.
- The Q panel is photographed at 12-hour intervals with a high-resolution digital camera.
- The product is graded according to the average percentage of the Q-panel covered with corrosion during the 60-day test period.The test results indicate that the TC-11 is a much better corrosion inhibitor than any of the competing products as presented below.

TC-11 offers 41 days of corrosion protection. The closest competitor offers 25 days of corrosion protection.
Penetration Testing
Penetration testing is a particularly challenging effort. It is a time consuming process, because it is necessary to fabricate bolted assemblies and to let them weather naturally for a period of time that is sufficient to generate a frozen fastener.
The following procedure was used to perform the penetration test:
- A 3/8-16 coarse thread steel nut was bolted to an steel bolt with 35-foot pounds of torque.
- The bolted assembly was allowed to weather for eight months.
- A randomly selected bolted assembly was placed in a rigid socket.
- The bolted coupon was pre-loaded with 40 foot-pounds of torque using a digital electronic torque wrench.
- One of the following penetrating oils was applied to the frozen fastener:
- TC-11
- WD-40®
- Discontinued Product
- Discontinued Product
- PB™ Blaster®
- The amount of time required for the penetrant to un-freeze the fastener was measured with a stopwatch. Un-freezing was indicated by a drop in the torque reading.
- This process was repeated three times for all five products
The penetration test results are presented below.
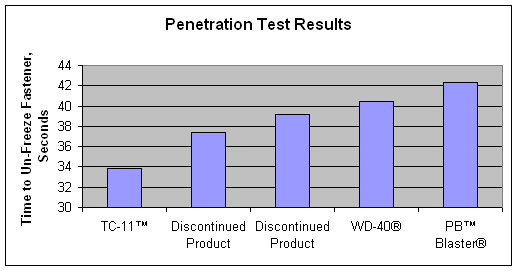
Compatibility Testing
In order for a bulk lubricant to perform effectively, it must be highly compatible with rubber, paint, and plastic. If the product is not compatible, it can have an overall negative effect on the reliability of the treated equipment, particularly the electrical system.
The most sensitive class of rubber, paints, and plastics is elastomers. Elastomers are flexible, which means that they are more subject to compatibility issues than rigid plastics or paint. Natural rubber, or Latex, is one type of elastomer.
Elastomers either expand or contract when they are exposed to solvents. Any type of dimensional change indicates compatibility problems. An ideal bulk lubricant would cause zero dimensional change in an elastomer, even after decades of exposure.
The bulk lubricant compatibility test was conducted using the following procedure:
One inch diameter test coupons were punched out of 12” x 12” sheets of the following materials:
- One inch diameter test coupons were punched out of 12” x 12” sheets of the following materials:
a. ½” natural rubber
b. ½” Buna-N
c. ½” expanded cell silicone
d. ½” Neoprene
e. ½” SBR
f. ½” Butyl
g. ¼” Hypalon
h. ½” EPDM - The thickness of the coupon was measured with a micrometer.
- The coupon was exposed to one of the following products:
a. TC-11
b. WD-40®
c. CRC® Heavy Duty Silicone
d. LPS® Heavy Duty Silicone
e. CRC®3-36
f. PB Blaster®
g. Corrosion-X®
h. Boeshield T-9®
i. Discontinued Product
j. LPS®-2
k. Corrosion Block®
l. Tri-Flow®
m. Prolong®
n. LPS®-3
o. CRC® 2-26 - The coupon was placed on an indoor counter with all of the other coupons.
- The thickness of the coupon was measured and recorded on a daily basis for two weeks.
- The thickness of an untreated coupon of each type of elastomer was measured and recorded on a daily basis for two weeks
- The measurements were converted to absolute numbers.
- The measurements were used to determine the difference in thickness between a treated coupon and an untreated coupon exposed to exactly the same environmental conditions.
- The differences in thickness were summarized.
- The products were graded according to the total amount of dimensional change over the two-week test period.
The compatibility test results are presented below.
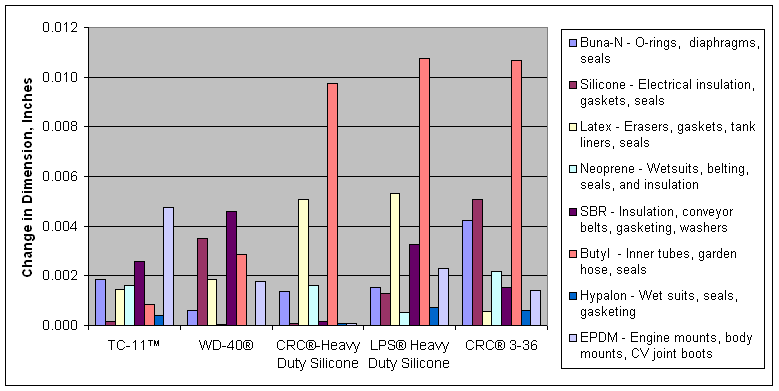
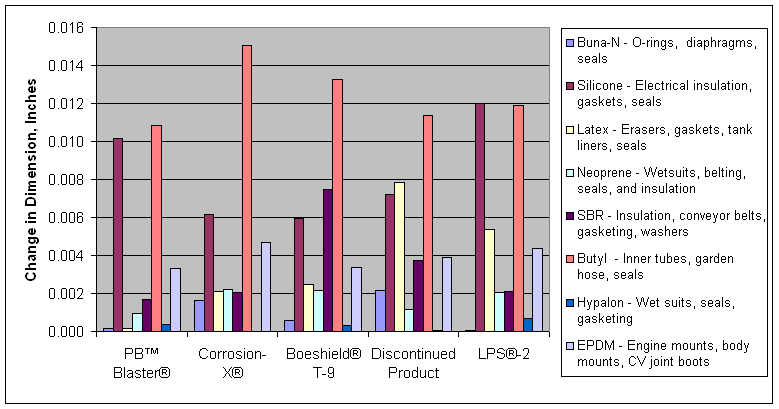
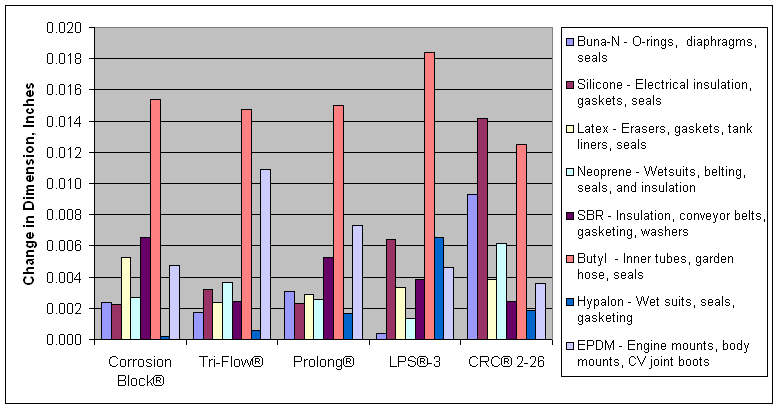
The compatibility test results indicate that TC-11 is the most compatible bulk lubricant on the market. This is a major factor in the overall performance of TC-11.